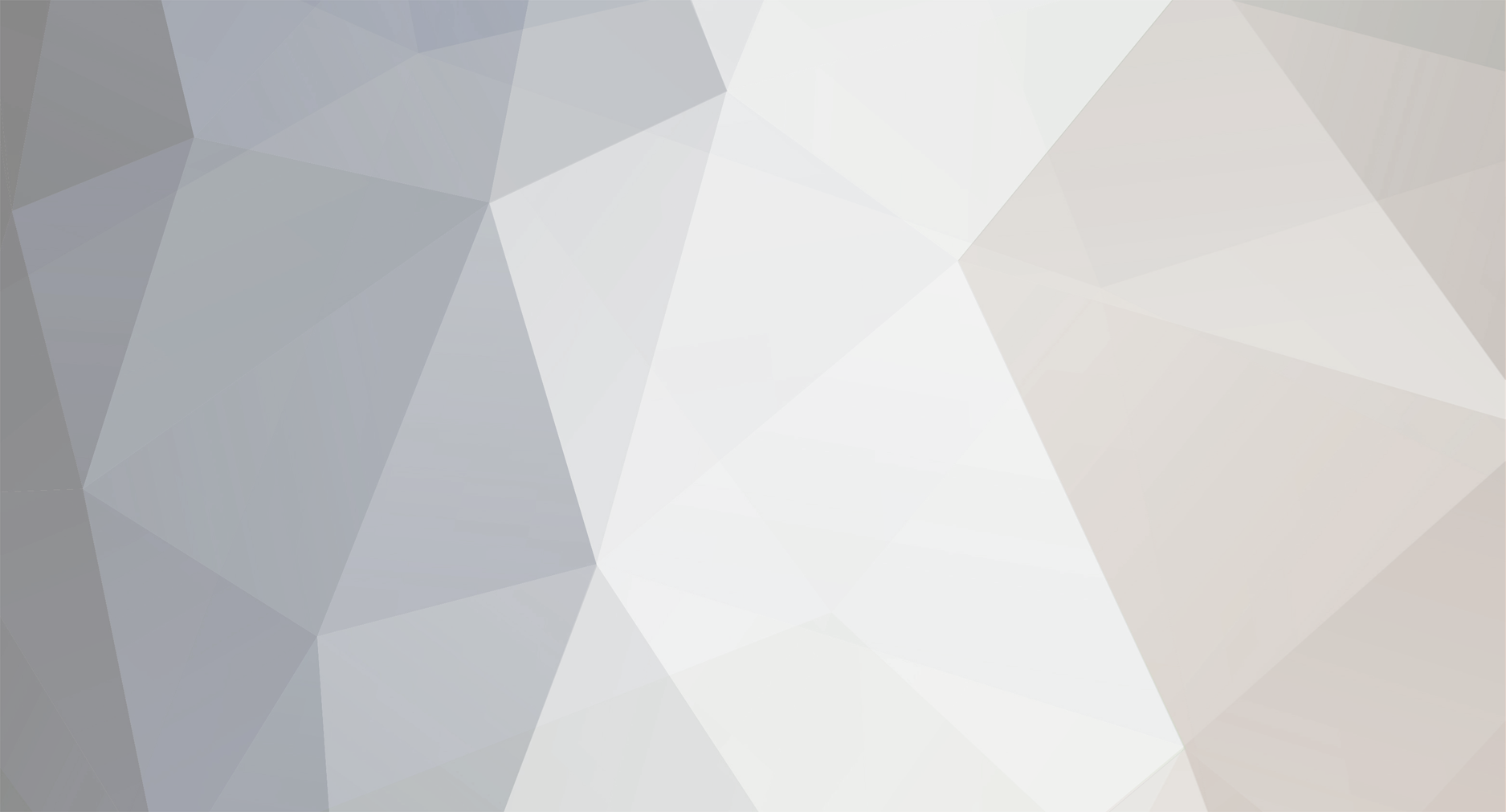

Rebelgolfer72
Members-
Posts
17 -
Joined
-
Last visited
Never
Personal Information
-
Location
Pittsburgh, PA
-
What DNA product do you own or plan to buy?
DNA200
Rebelgolfer72's Achievements

Member (2/3)
0
Reputation
-
I for one would love to see a preheat for non-TC modes. Have it as a percentage of set wattage (I.e. 5, 10, 20% boost etc). ProVape and YiHi are doing it, so I would think that the most advanced board out there should be doing it as well.
-
Feature request - power mode boost/ramp up
Rebelgolfer72 replied to Rebelgolfer72's topic in EScribe, Software and Firmware
I do notice that . And thank you for the clarification. I think that the reason it "feels" like it is ramping up is I've become spoiled by the preheat in temp mode as well as other mods that have boost functions. With that said, I still would like to see the following enhancements: 1- Preheat/boost curve available in power mode 2- the ability to set the preheat amount as a percentage of the set watts (both in temp mode or power mode). Reason being, it would keep the preheat working as expected when changes are made to the set wattage. -
I would venture a guess, that the default mod resistance is assuming stainless 510, which is standard...but the hcigar uses brass for the negative which when clean has a lower internal resistance, and silver plated copper center pin (very very low resistance).
-
I got the same reading yesterday, but I was running a little experiment (and it mostly worked!) I wanted to fool the board into thinking the coil never reached the set temperature, so I could get the preheat function with Kanthal. So I used an exaggerated curve, locked the resistance, and set the temp to 600°, and yes, it fired a Kanthal atty at my preheat wattage for the specified time, then dropped back to the set wattage... The only thing that didn't work (and I didn't care about) was the temperature it was reading...I got the 3554° number. Thinning its some .error. Or "overflow" value.. Which for my experiment I didn't care, as I was t wanting temperature control, just the preheat
-
Feature request - power mode boost/ramp up
Rebelgolfer72 replied to Rebelgolfer72's topic in EScribe, Software and Firmware
I notice in power mode that the power does t instantly fire at the set wattage, but ramps up, hitting a mid point first. I would love to be able to turn this off. On the same line as the first request, I,would also love to be able to set a preheat for power mode...but instead of a fixed wattage boost, perhaps make it a percentage of set wattage: for example if wattage set to 40w, and boost set to 20% for 1 second, it would fire at 48w for a second, then start firing at 40 for the length of time the button is held. Likewise if set to -20%, it would fire at 32w for a second before kicking up to 40w -
I had one that failed a few weeks back. Had it for 5 days where it worked fine, then it died mid-puff. Replacement arrived on 10/17, as well as a second one I picked up arrived on 10/19. Been using these exclusively since arrival to try and draw out any early life failures on these. So far so good with 5/3 days respectively on the units. Let's hope the one that died on the 10/1 is the only one.
-
If how BaporShark did the fire button LED on this the same way they did on other DNA boxes,,the LED on the switch is coming directly tapped off of the battery. You cold remove the board completely, and the switch LED would still work
-
I've found that running the latest version of VirtualBox seemed to work better than VMWare Fusion. Had slow transfers and timeouts under VMware, but VirtualBox (and the new USB enhanced package that you can install with it), had very fast transfers -- matching those on a native Windows PC
-
Please put a Temp Lock option in software!!!
Rebelgolfer72 replied to Droopydroors's topic in EScribe, Software and Firmware
Ideally, to handle all wire sizes, ther would have to be 2 different (selectable) methods for controlling temperature. The straight power modulation like it has now works best from my experience with 28g and smaller wire (single coil). For heavier wires, I believe a pulsing type method of heating would work the best-- but then you would have folks that wouldn't like the fact that they can feel (or hear) the pulses in the Vape. FWIW, I had 0 problems using temp control with stock Aspire Triton coils (0.4?, 24g, 317L stainless)- however I was conservative with the preheat, used the Sam wattage I use running in power mode (36.5W), and set th temperature at about 440°, just to catch the tail end of longer vapes....in fact, this was probably the best Vape I ever had. Now I just need to get my DNA200 repaired/replaced...been almost a day, and I alread miss it! -
Is Evolv handling the replacement of boards that are dead in commercially available units (I.e. Hcigar etc), or does that have to be handled by the vendor that the mod was purchased from? I don't mind going back to them, however if there was a bad run on boards, or the Mfr. is doing something in the mods to increase the likelihood of this problem recurring, I'd hate to simply swap the dead box I have now for another off the shelf only to be in the same boat again next week.
-
My hCigar VT200 did the same thing to me on the way home today. Just received it 5 days ago, and barely used it more than an hour or 2 each day (using other devices), and never over 40w continuous (briefly had preheat at 55).
-
Please put a Temp Lock option in software!!!
Rebelgolfer72 replied to Droopydroors's topic in EScribe, Software and Firmware
I believe the devil is in the details here. The nature of the type of coil that you are using (I think you said some type of "Clapton coil" variant...which now makes the heating wire into a heating "cable"), relies on the oxidation of the wire to insulate the various strands and wraps of the wire from each other. In reality, you are only directly heating the lower resistance core wire, and the current flow through the longer, thinner wraps that are in parallel to it is minimal. As a result, these wraps are not being heated by the current, but actually getting most of their heat indirectly from the hotter core wires. So by nature, the resistance of the heating cable is not extremely stable in and of itself. This also compounds the stability of the connection to the atty. I really believe that this is one of those cases where people are asking too much from the boards in terms of regulating temperature. A close second to this is the use of long, heavy gauge wire. These heavier wires require a ton of energy to be dumped in to them in order to heat them. Once they get close, or overshoot, the only thing that can be done is cut power -- there is no way for the board to stop the heat or reverse it. It's like trying to stop a locomotive vs trying to stop a Prius. By the nature of things, I believe that the shorter and thinner your coil wire is will yield the best accuracy in TC, as it will heat faster AND cool faster so will respond much better to the power modulation used to control the temp. An analogy to this would be the difference in how a light Corvette handles a fast, winding road vs how a heavy pickup truck with a 12" lift and oversized tires would handle the same road. From my experience years ago in programming the automated cycles of resistance welding/brazing machines, I can tell you that you have to approach heating metals with more mass quite differently than lower mass materials. With lower mass materials, you can simply fluctuate the power to regulate the temp. With materials of higher mass, your best accuracy isn't with consistent and modulate power, but by pulsing the heat-- having alternating short pulses to heat, and rests or cooling cycles between the pulses-- allowing the mass of the metal to stabilize. I've also found that with trying to use the DNA200 with stainless, by taking the approach of using the same power setting I would in power mode, using a conservative 20% boost in that for a short preheat and adjusting the temperature limit to really only take the overheating that would occur at the tail end of the puff out works the best. I approach it like I would with compression/limiting in the music/broadcast industry.