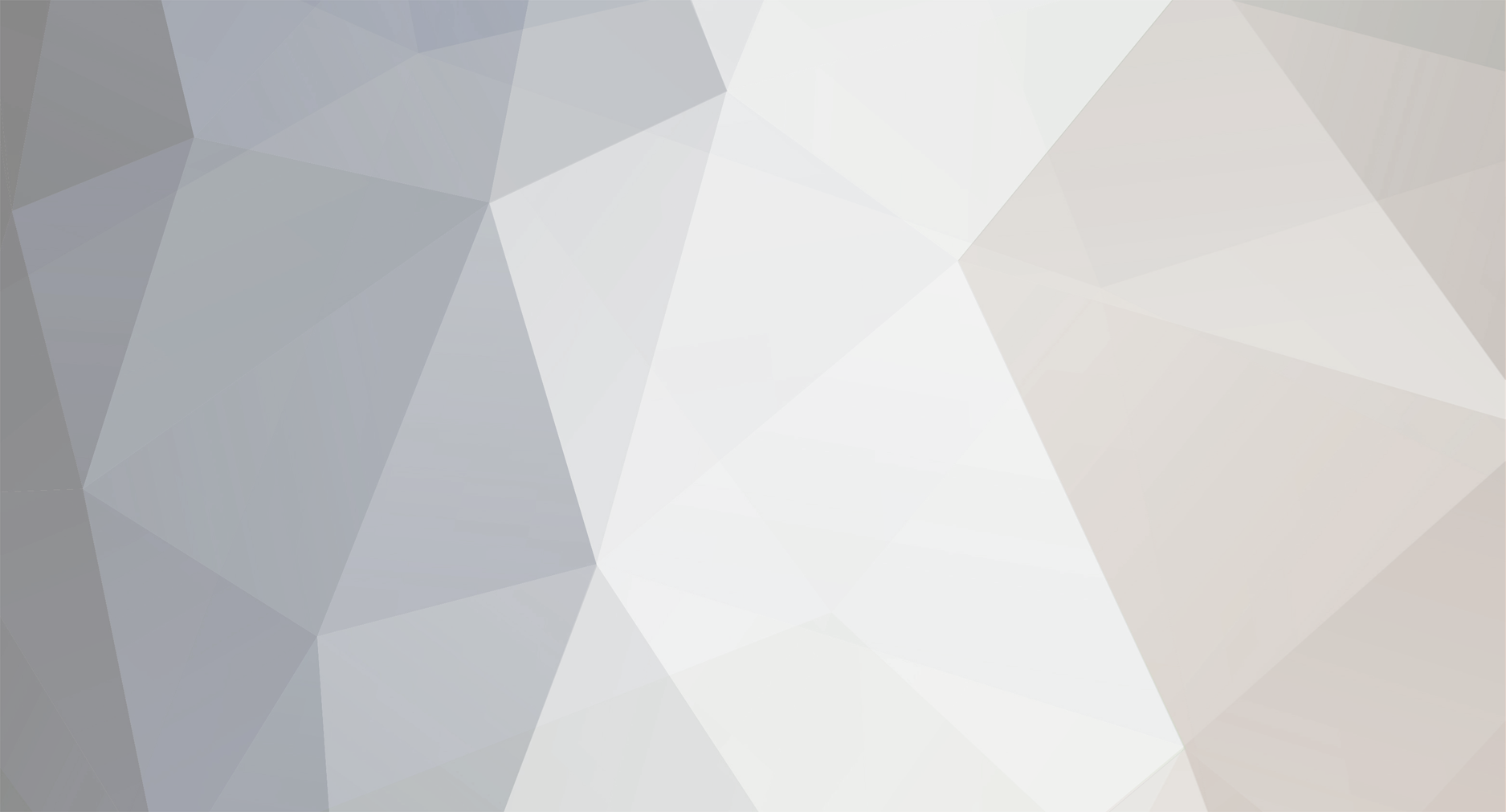

Mad Scientist
Members-
Posts
247 -
Joined
-
Last visited
-
Days Won
1
Content Type
Profiles
Forums
Downloads
Everything posted by Mad Scientist
-
Ti Temp. Protection lighting my cotton on fire
Mad Scientist replied to Sticky907's topic in General Discussion
I would first check to make sure cold atty resistance is stable and repeatable using atomizer analyzer. If cold resistance is read as higher than what it actually is, temps can go to the stratosphere. Start checking connections, including on the atty, screws tight, etc., 510 clean, good ground between 510 and board . . . Another thing that will light up an atomizer is TCR too high. Make sure the correct (or at least sane if there's no way to verify for the specific wire) normalized values appear on the profile screen for the atomizer. Is the wire you are using SSV? Their curve is different from Ti grade 1. If you're using Ti grade 1, the TCR curve may be too high. Use the steam engine curve. Another thought is possibly high static resistance of the atomizer. Attys with an intermediate connection (like replaceable coil assembly) or adjustable pin seem to be the worst on this. You may have to adjust the TCR to compensate. What atty are you using? -
Now that is machinist porn lol. What tools/machines did you use? Looks like every little detail finished to nth degree. Beautiful.[/QUOTE] Thanks Mad Scientist. My missus bought me a Proxxon micro mill last year for my birthday last year and it stopped working just after this birthday. I used this years birthday funds to buy a swig 1XL mill/drill and it's been great. I also use a dremel and needle files to finish off.[/QUOTE] Nice. I have to see if Santa might be willing to spring for something that expensive lol. Your experience shines through though. I am no expert machinist but I know enough to know that ain't easy.
-
Need a "like" link as on ECF lol. Thanks, like.
-
Another technique would be to just use a large loop from post to post rather than coil the wire. The difference just from free air cooling is surprisingly significant.
-
Mod Crate 1590A CNC
Mad Scientist replied to Podunk Steam's topic in Connectors, Components, and Accessories
Looks good. I know photos show a lot more texture than what it actually looks like in hand (at least with my eyesight lol). Superb engineering job. The hinged doors are over the top! -
Step one always seems to be post a screen from device manager showing the cell and pack voltages. Can you do that?
-
Now that is machinist porn lol. What tools/machines did you use? Looks like every little detail finished to nth degree. Beautiful.
-
Gorgeous. Nicely done.
-
Nice. I wish every atty had posts like velocity (I assume that's what it is).
-
Thanks, that is really good to know. On my next build I plan to try superglue or hot glue a small piece of cardstock as a strain relief at the glass interface to the flex circuit. I think you have the failure mode spot on. Unfortunately, I don't have an uncommitted DNA 200 board . . . For now.
-
Looks good. Do you crease it hard? It does have a generous radius in the bends as an end result but I understand you to mean you need to crease it hard to get it to hold that shape? From your conclusion that it's the attachment point at the glass as a weak link to avoid bending (which makes perfect sense) I wonder if adhering a thin piece of stiff plastic maybe 1/2" or so leaving a 1/4" on each as a strain relief at the interface of glass to flex would help reduce so many screen failures.
-
I'm the guy who retrofitted the Xcube 2 with the "fire bar" thing on it. My entire screen moves a couple millimeters every time I fire but there's at least a half-centimeter radius to the bend. No problems so far but I guess I need to cross my fingers lol. It's supposed to be a flex circuit and they must have a performance spec for bend radius. A typical, conservative "safe" bend ratio for a single bend is 5:1 radius to material thickness (often even less but that's conservative). For a dynamic bend it has to be more but I've seen figures quoted of only 3mm even for multilayer, so I should be OK with the radius I have. In any case, just folding it over sharply, even once, might be a bad idea.
-
dna200 inside a vaporshark vaporflask? I think so.
Mad Scientist replied to iandvaypes's topic in Installation and Assembly
Wow, very well done. A lot of work but you did it! -
According to the manual, a recovery operation is logged to evolv so they know it happened (it shouldn't happen unless something went very wrong somewhere). I agree with Boss; submit a ticket with Opus so any problems down the road are covered.
-
I bought about a half dozen of these for another project that didn't pan out and have them all over the place. https://www.sparkfun.com/products/11456 Cheap and they work fine for charging.
-
You should see the layer of dust on the other one. Can't remember when that one was from but from the looks of it, a long long time lol.
-
Default function of up down buttons
Mad Scientist replied to blueridgedog's topic in General Discussion
The thing is, a big build that needs, say, 120 watts to reach 450 F can be throttled back by limiting either wattage or temp (or both but no real point in that). I believe the end effect would be the same. To noodle it out, say 50 watts on that build will max out at 410 F and that 50 watt vape is all you want in terms of enough vaper. Just set temp to 410 for equivalent effect and leave the power setting where it was at 120? -
As a novelty item it's a great idea. Several of my friends are rabid Star Wars fans. As an actual usable mod, in my opinion, not so much.
-
Default function of up down buttons
Mad Scientist replied to blueridgedog's topic in General Discussion
Yup -- that's why the buttons should be configurable. Different strokes . . . -
Default function of up down buttons
Mad Scientist replied to blueridgedog's topic in General Discussion
Agreed -- another vote for being able to configure the buttons to adjust temp. Would also like to be able to display temp in large font with wattage being the tiny font. Would also like to be able to set the temp increment for each button press. Sometimes 10 degrees is too much either way and a computer isn't handy nearby to tweak the temp less than 10 degrees. The temp control on DNA 200 is so spot on that wattage has become almost irrelevant as long as it is set to enough. The performance has finally made it to true temp control leaving temp protection behind in its wake. The user interface can now evolv (!) to reflect the new level of performance the board delivers. I finally got a mod put together with DNA 200 board inside in a portable package that I trust enough to carry around all day. After using it as an all day mod, this board is what all other mods want to be when they grow up lol. (can you tell I'm happy with how well it works lol) -
You may need to experiment with wattage and temps to get the vape you're looking for. What I've sort of ad hoc observed is that attys with an intermediate connection (like with a separate replaceable coil assembly or loose adjustable pin) have a higher static resistance which, at least for me, has always resulted in a hotter vape. The mod expects that static part of the resistance to increase with power input and when it doesn't, the dynamic resistance of the coil has to increase by getting that much hotter before the mod "thinks" the coil is at the set point temp. But at a point, enough extra static resistance will also start to affect the mod's wattage calculations so I could also see a cooler vape as a result. In both cases, the mod is doing what it's supposed to, but less than perfect internal connections within the atty affect the mod's ability to accurately calculate temp and wattage at the coil. I'd suggest increasing the max wattage to at least around 35 or 40 and then adjusting the temp to suit. This should eliminate or at least reduce the static resistance issue from the wattage calculations. Adjust the temp to suit and then see where you're at. You can set a profile for each atty to deal with these types of differences.
-
Solder type at contact points?
Mad Scientist replied to Podunk Steam's topic in Installation and Assembly
Yeah, you're talking about soak temps and I think you're still low. A full soak is heat the metal through and through, not touch it at a temp for a few seconds with heat transfer through multiple parts and mediums. You can't get a full soak on that spring anywhere near to even just 700F witth a soldering iron, even applied directly to it. The iron isn't hot enough, the heat transfer is not efficient enough and the amount of time is not long enough. Also, if the spring used were adversely affected at 250 F, I would be concerned about heat transfer from a 450F coil a few millimeters from the pin as well as up to 200 watts through the wire and pin transferring the heat to the spring just as much as 400F or 450F soldering iron at the pin and end of the wire. Etc. I guess I just don't understand your obvious hostility to the concept. If it's that big a deal to you, apply heat sinks to the spring and be happy? I've done it the exact way I describe with no issues so I feel comfortable suggesting the method. I learned the idea from another knowledgable person here. If it doesn't work for you or you don't like it, don't use it. Cheers. -
Been sitting on the side of the bench just about right there since circa May 2013 lol. Also have a pack from overseas toward the back of the bench not seen in the pic. They've been there so long I can't throw them away.