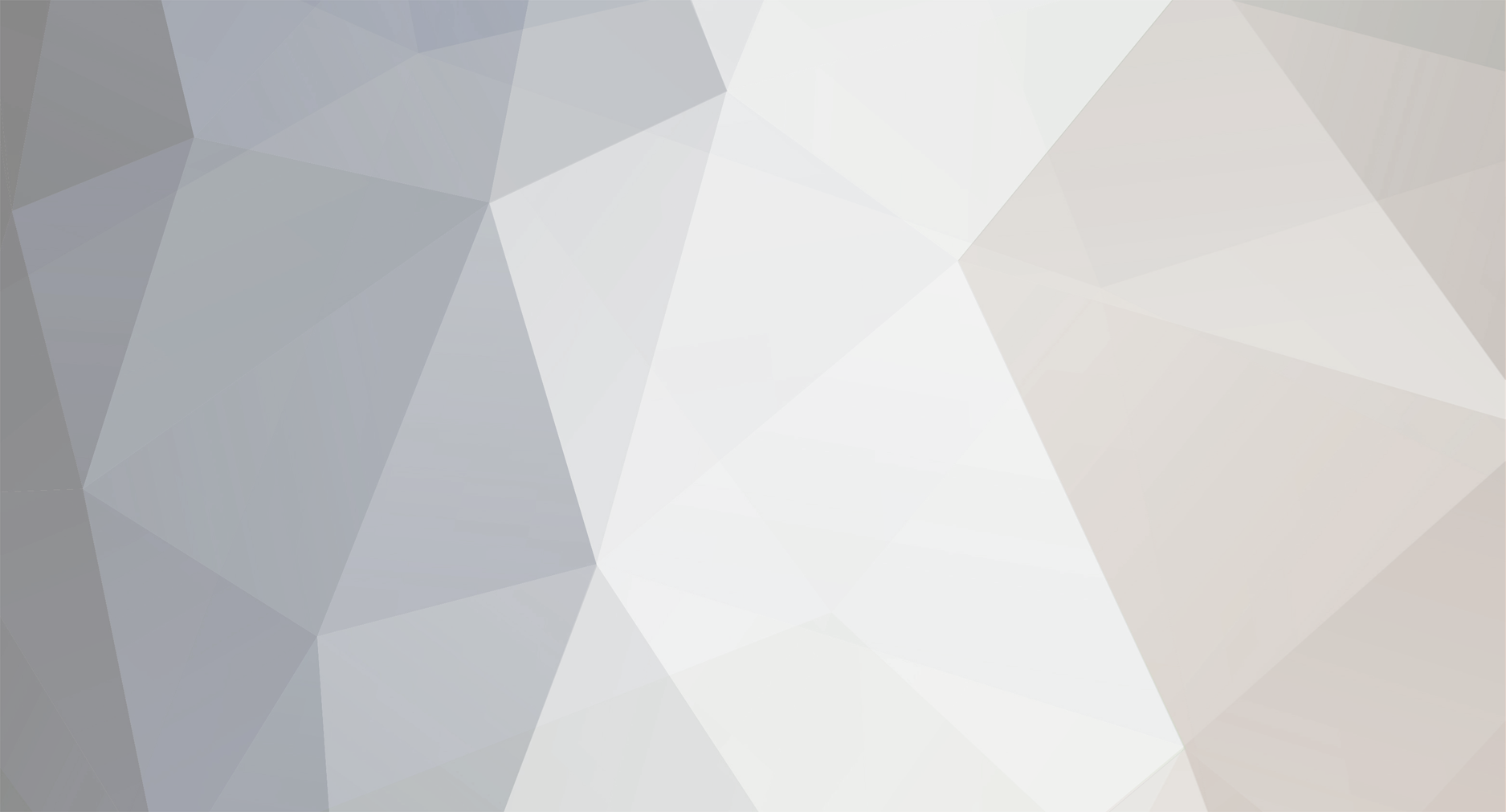

Mad Scientist
Members-
Posts
247 -
Joined
-
Last visited
-
Days Won
1
Content Type
Profiles
Forums
Downloads
Everything posted by Mad Scientist
-
[Feature Request] screen indicators by profile
Mad Scientist replied to elgabo's topic in EScribe, Software and Firmware
What I do is set up each profile so the tenths in watts is the profile number. So profile 1 is set to xxx.1 watts. Profile 2 is set to xxx.2 watts, etc. If you use temp dominance you can do the same thing with degrees. Profile 1 is xx1 degrees, profile is xx2 degrees, etc. By doing that, you can tell at a glance which profile is selected. -
Wow, led colors as a setting in eScribe. Very interesting. Look forward to see what mod makers will do with that.
-
What is the resolution of the resistance measurement?
Mad Scientist replied to Bobby's topic in DNA 200 and 250
What is the cold resistance of your stainless coil? You could try wrapping your coils with increased cold resistance (within reason) to "leverage" the low TCR of stainless. The actual resolution and practical resolution are going to be different (likely very different). At a point, electrical noise in the environment will drown the measurement. Even measuring to "just" milliohms accurately is not a trivial task. -
140W and 30ml isn't pushing the boards. They can handle over 200W but battery safety makes 200W the practical limit. I have no way to know if your iron was the common denominator but it is something almost always overlooked. ESD parts damage shows up in unexpected places often with odd symptoms. A part can be weakened but still function, and then fail under long term stress or just fail unexpectedly for no apparent reason. Again, I have no way to know if that's what's causing your failures, but four dead boards would lead me to look for a common denominator in my shop. A cheapo soldering iron that's not ESD safe would be first on the list of things to never use again. The one you linked says it's ESD safe and has good reviews, so hopefully it lives up to its description.
-
As another thought, your soldering iron itself might be the issue. I've used irons with enough leakage that I could feel a slight shock when touching the solder to the tip (and the iron with its controller quickly placed in the junk parts pile). If the iron isn't ESD safe, that could be another issue. What iron are you using?
-
I think this discussion might be helping to refine the questions, and I think maybe it has been answered. So if I'm understanding the answers correctly . . . if the DNA 200 detects data lines, it will still negotiate with the hub for up to 1A of charge current? As a result, it is not necessarily malfunctioning if it draws 1A charge current from a PC that is capable of supplying 1A or more? If the DNA 200 draws more than 1A of charge current it is malfunctioning?
-
Have seen some questions asked about the current draw on a USB port when charging so wanted to get the solid scoop. My understanding of the specifications is that DNA 200 USB current draw is specified to limit at 500mA if data lines are detected and 1A if not (assuming USB current limit is set at 1A in escribe). So to the question: if a DNA 200 draws significantly more than the 500mA and 1A as specified in the respective operating conditions as set forth above, what is the explanation? As a general proposition, operating outside of specification is a malfunction but can more light be shed on what is likely going wrong in each circumstance. Thank you.
-
Ok, this is a total stab in the dark but since you have 2 doing exactly the same odd thing, is it possible that your USB power block switching supply can't source the low current draw when the batteries get close to full charge or go into "balance mode"? Maybe some other odd characteristic of the power source? I'd try increasing the charge display brightness so you can see it, displaying the charge current draw on the charging screen and comparing behavior with different brands of USB power blocks and USB power sources you have available. Also maybe watch the charging process in device manager when it's connected to a PC. Only thing that comes to mind at the moment.
-
@Wibberly, that is a work of sheet metal art. Looks fantastic.
-
I think that both failed boards should both go back to evolv for a failure analysis, perhaps along with the USB power block associated with them. I know I've seen more than one person with multiple failed boards and that makes me wonder about a common denominator -- like for example a USB power source with some characteristic that destroys boards. If that were the case, unless the USB power block is doing something outrageous (always a possibility), maybe there's a way to make the board more tolerant of funky power supply issues. Just one thought. Coincidence and "bad luck" are always possibilities. I see that evolv is always working to improve the product so I'm guessing they'd want to see the boards to try to figure out what may have gone wrong with both of them.
-
I'm pretty sure it is undesirable (i.e. reduces cycles before the battery won't hold a decent amount of charge anymore) to allow a lipo to fall below 3V under load. The 3.09V cell cutoff was intended to follow that thinking with a very small safety factor of 0.09V. You could reduce the cutoff voltage setting to obtain more out of the battery before soft cutoff but your number of charge/discharge cycles before you need to replace the battery will fall. The best measure of battery charge status is voltage under (known) load. I don't think, IHMO, that refining a scheme for cell cutoff based on resting voltage is a step forward.
-
My recollection is "resting" voltage is around 3.6 to 3.7. Of course the voltage under load is the low voltage cutoff which I have not adjusted (still at default of 3.09).
-
I have a new mantra. Increasing applied power increases temperature; increasing temp setting increases applied power lol. I think it's silly that an unfortunate comment in a pbusardo interview has "evolved" into a religious doctrine. That said, having used a mod that had only a temp setting without being able to limit power, I don't like that method. Temp control is generally very accurate but the technology is still far from perfect. We definitely need the ability to set limits on both temp and power. The only issue is some prefer to adjust one more frequently than the other. The present UI state machine does not take that difference in preference into account. It will likely be a pain but evolv needs to change the UI state machine to be table driven and allow us as users to modify the table, or at least allow us to modify some entries in it.
-
I have 5 "married" sets of inexpensive 18650's and not one of them behaves as poorly as I've seen described in this thread. I set my home grown double 18650 DNA 200 mod to 2 cell, set the Wh to 17 and I can vape beyond when my battery meter reads 0% without any low battery message. I have preheat set to 100 W 1 second, punch 5, watts 75, temp between 450 and 490 as the mood suits me. These are the batteries: https://www.fasttech.com/products/2913000
-
Lol. Good thinking!
-
Hi James, Would it be possible to get an updated comprehensive list of available commands? I remember you guys added the up / down button presses as commands (I'm almost positive I saw a post on that -- and I thank you for doing that) and looks like I'm finally approaching a point where I'm going to need them. As always, thanks very much.
-
Here is my recommendation but it will take some patience. You indicated that the new battery is already on its way so might as well wait for the new battery section to arrive. Test its operation with the new battery. If the fuse is indeed blown, of course it won't operate. Contact the vendor, explain that even with the new battery it's not functional and ask to return the unit and battery for exchange for a functional unit. If they won't help you out, open a ticket with evolv. Replacing a tiny surface mount fuse is not a task for the uninitiated lol.
-
how many amps does each cell charge at?
Mad Scientist replied to Spector NS5 RD's topic in Batteries and Charging
I agree with awsum140. At least the way my mind works, it's easier to think about it in Watt-hours. A one Amp USB charger delivers basically 5 Watts. Conversion losses and charging efficiency are a bit of a wild guess on my part but it's darn close to 100% for a lipo -- lets be conservative and say 90% total efficiency. Also a "dead" battery isn't actually "dead" but more like 80% discharged. So a 10 Wh battery would need 5 x 0.9 x charge time = 10 x 0.8. Solving for charge time yields charge time = 8 / 4.5 = about 1.8 hours to charge. Substitute the Wh rating for your battery for the 10 in the example and you can estimate charge time needed. -
Odd behavior. Looks like a decent amount of power at the 510. Just curious, if you leave an atty on it, will it drain the battery? You might have to RMA it.
-
Want to get another DNA200-suggestions?
Mad Scientist replied to Conanthewarrior's topic in DNA 200 and 250
It can be opened but doing so requires carefully lifting one of the carbon fiber panels to access two screws. Other than replacing a tired, old battery that needs to be replaced, it's likely not practical to open and close it more often. I hope for about a year of daily use before the battery needs to be replaced. -
I would stop messing with the old battery housing if you think your soldering skills are rusty. It will take some willpower but wait until the new battery section arrives. The risk is if you do something that damages the board then you have a real problem. From what you've said it seems like it could be the fuse but you say you've tested the fuse? Let us know how it works or what it does when the replacement battery section arrives.